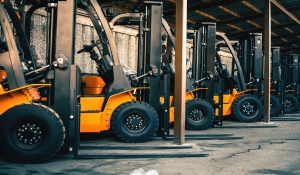
Today, June 14, is National Forklift Safety Day. This day brings awareness to those using forklifts in warehouses, manufacturing, and other industries. Having a day dedicated to forklift safety may appear trivial, but there are close to 100,000 forklift accidents each year. Proper training plays a huge role in preventing accidents.
In order to share as much information as possible about forklift safety, Alexa, our Content Specialist interviewed Jordan, an Instructor and Inspector at CICB. Jordan has prior experience as a forklift operator and also teaches CICB’s forklift courses.
The interview consisted of two parts: the first part was analyzing a video of a forklift accident, and the second was a discussion of Jordan’s observations and experiences.
The Analysis of a Forklift Accident
Back in 2016, a massive collapse occurred in a food distribution warehouse in Shropshire, England. Thankfully, there were no injuries or fatalities, but the damage to the products and shelving units in the warehouse were was immense. The entire accident was captured by security cameras at the warehouse.
Alexa and Jordan watched the video of the accident together, while Jordan provided commentary on his observations.
In the video, the forklift operator was backing up and trying to maneuver between two employees with what appears to be
a large cart. The operator miscalculated the amount of space he had, and ended up tapping one of the shelving units, which created a domino effect throughout the entire warehouse.
Many comments on YouTube claimed the shelving units in the warehouse did not appear sturdy enough, and that a small bump should not have caused the entire unit to collapse.
Jordan disagreed with those comments, however. “What the operator did is similar to side-loading a crane.” He stated. “The shelving units are designed to hold items vertically. Even with just a small tap, the unit is no longer vertical, and it is not designed to move in the direction it was pushed.”
Jordan believes there were two safer options that would have prevented this accident. First, the operator could have stopped the forklift momentarily to have a conversation with the two employees. He could have asked them how long they were planning on being in the aisle. The employees could have moved, and he would be able to safely navigate through the aisle.
If the employees were unable to move their cart, the operator also could have gone back in the direction he initially came and turned down a different aisle. Both of those options would have prevented the collapse that occurred.
Forklift Accidents
After analyzing the video, Alexa asked Jordan about forklift accidents he has witnessed/heard about. Jordan stated, “Most accidents come from operator error. Operation often becomes too routine, and the operator begins to feel complacent.”
OSHA’s 29 CFR 1910.178 standard requires forklift operators to be trained every three years. Jordan believes it should be changed to two years, however.
From his experience, the majority of forklift accidents he has witnessed were due to backing up into something. Bad behaviors can form and become new behaviors. For example, a forklift operator may have backed into a shelf before, and nothing happened. The operator is now less careful since he/she is more confident that an accident won’t happen. When the operator backs up into the shelf again, it collapses.
It is important to follow the proper standards and safety protocols at all times. If an operator is continuously using shortcuts, their luck will run out eventually, and an accident will happen. Following all safety procedures is the only way to prevent an accident.
Forklift Training
Proper training is paramount. Even though a forklift may appear simple to operate, trainings should last at least a full day - some companies will only spend 15 minutes training their operators. By giving operators a “crash course,” they will not understand the standards, common hazards, or ways to prevent an accident. Operation is more than knowing how to drive a forklift; it is about knowing its safety components.
Even though proper forklift training may appear expensive, the upfront cost will save a company. Jordan stated, “If you put money into training and look at long-term accidents, it is much more cost effective. OSHA records incidents and if that number is too high, companies will not hire you for a job.”
In other words, if a business sends their forklift operators to other job sites, they will have a difficult time receiving business if too many accidents are recorded.
CICB offers forklift training courses. This training is one day and ensures all operators will leave with ample knowledge and experience. The course begins with videos to introduce the training, then the trainees will have time to practice on forklifts. This training is only offered on a company’s site, so the employees will be comfortable with the exact equipment they will be offering on the job.
After practice time, there will be time spent in the textbook which discusses the standards for forklift operators. A written and practical examination will be given after all material is covered. If either of these exams are not passed, another day of training is highly recommended.
The practical examination consists of a course. The operator will navigate the course, pick an object up, and then set down the object at another location. Those who successfully complete the course should be able to perform their job safely and have a lower risk of accidents.
Forklift Inspections
CICB also teaches a course for forklift inspections. Poor maintenance is also a cause for accidents, and it is important to ensure that your company’s forklifts are safe for operation. In addition to teaching operators, Jordan performs forklift inspections. His most common findings are bent/damaged forks and hydraulic lines, bent axels, poor electrical systems, and damaged tires.
By operating a forklift that has flaws, the risk of an accident significantly increases. Accidents can occur to objects in addition to employees.
Jordan recalled a time when he operated a damaged forklift. The tires needed to be replaced, which caused the forklift to jolt upward. He was using the forklift to transport X-Ray equipment at a hospital, and if he operated at normal speed, the equipment would get damaged from the constant jolts. To prevent this, he had to reduce his speed significantly, and the job took over twice as long to complete as it should have.
The cost of replacing the tires on the forklift may have seemed like a lot to the business. However, replacing the x-ray equipment would have cost far more than the tires. In addition, the money spent would have saved time on the job.
The Importance of Forklift Safety
The factor that we cannot stress enough is how preventable accidents are. Properly training employees and maintaining equipment may appear costly, but the upfront cost outweighs the long-term cost. Employee injuries and equipment/property damage is something you do not want your business to encounter.
CICB offers a Forklift Train the Trainer course to provide a cost-effective method for training your employees. Instead of bringing CICB to your site each time you need to train operators, we will build a program for your trainers. This allows your staff to provide the proper training that operators need.
After training, forklift operators must continue with the safe practices they learned. Taking shortcuts and driving too fast will increase the chances of an accident or injury.
Jordan wanted to end with one final comment toward businesses and employers: “At the end of the day, patience and teamwork will go a lot farther than recklessness and speed.”