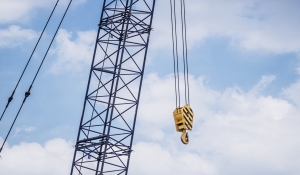
Each industry has their own standards that must be followed. There are also certain standards for each role in the lifting industry. For example, riggers have their own set of standards that may or may not be the same as crane operators.
As an employer or supervisor, it is important to be up to date with the standards in your industry, as they can change from time to time.
If OSHA visits your job site and a standard is not being followed, there is a high probability that a citation will be issued. Violations often come with hefty fines, so be sure you are not costing your company dollars that could have been saved. In this blog post, we are going to discuss three standards: two of which apply to crane operators, and one which applies to riggers.
OSHA 1910.66 (Standard for Crane Operators in the General Industry)
The first piece of information from this standard states that the crane operator must be designated by the employer.
OSHA’s definition of designated varies across the standards, so it is important to be sure that your employees are designated based on the appropriate standard for your industry.
For the general industry, a designated person is approved or assigned by the employer to perform a specific type of duty or duties.
Generally, however, designated is defined as a person who is qualified and appointed by an employer for that specific task. (For example, an employee that is designated as a crane operator is not automatically also designated as a rigger. They would also need to be qualified in rigging and appointed by the employer.)
In order for an employee to be considered qualified, they must have extensive knowledge, training, and experience. They also must have demonstrated their ability to solve or resolve problems relating to the subject matter.
In addition, this standard also discusses training for crane operators. OSHA states,” Employers should use both on the job training and formal classroom training. The written work procedures used for this training should be obtained from the manufacturer, if possible, or prepared as necessary for the employee’s information and use.”
Although hands-on training is beneficial in numerous ways, employees should also have formal classroom training, whether it be through an agency or in-house. (CICB offers Train the Trainer programs which teach supervisors how to train and qualify their team.)
It is also important for the training programs to teach employees basic inspection procedures, so they can determine if platform equipment needs to be replaced or repaired.
In addition, emergency action plans should also be discussed during training sessions. Education prevents accidents, and in case an accident does happen, lives will be saved if the employee is taught how to handle the emergency.
Finally, when the training is complete, the employees should be required to demonstrate their understanding of safely operating the equipment.
OSHA 1926.1427 (Standard for Crane Operators in Construction)
Keep in mind that the standards apply to how the equipment is used, rather than the company’s main line of work. A company can operate in the general industry while also performing construction operations. Construction can also be the repair of existing facilities, so it is crucial for the employer to understand which standards to adhere to.
In this case, each operator must be
1.trained
2.certified, and
3.evaluated before operating equipment.
For an employee to be documented as certified, they must hold a license from an accrediting agency, such as the CCO. CICB offers preparation courses for CCO Examinations, which can also be used as training. Once both the CCO written and practical exams are passed, the operator will be issued a card that lists their certification(s).
After the first two steps are complete, the last step is for the employer (or a representative of the employer) conduct an evaluation. Keep in mind that a certification states the employee is capable of operating a crane; it does not state they are an expert.
For example, when a 16-year-old takes and passes their drivers test, they are capable of driving a car. However, they are not as experienced as their parents who have been driving for 20+ years. A certification is similar to a driver’s license.
When the employer conducts the practical evaluation, they will ensure the employee is capable of operating the crane. The employer will look for demonstrated skills and knowledge, the ability to recognize and avert risk, and that the operator can operate the equipment safely.
If the operator will be conducting blind lifts, personnel hoisting, and/or multi-crane lifts, the practical evaluation should also include the ability to perform complex hoisting activities. Once that last box is checked, then the crane operator may begin performing the job without assistance.
One final important note to remember is that in both general industry and construction, a qualified person must perform annual inspections on the crane in use.
A qualified person is an expert and has either taken formal training or has multiple years of experience. CICB provides inspection courses, as well as inspection services. The inspection must be documented.
ASME B30.5 (Standard for Cableways, Cranes, Derricks, Hoists, Hooks, Jacks, and Slings)
Although this standard also applies to crane operators, there is an important section for riggers that has been recently updated. This also applies to both general industry and construction.
According to the standard, “Rigger qualifications shall include evidence of completion of a written and practical examination. The examination must cover: selection and use of slings, rigging hardware, and below-the-hook devices, standard hitch application, estimation of load weight and center of gravity, angular loading on rigging components, load movement potential while suspended, and the applicable inspection and operating practices.”
This standard will officially take effect in December 2022. If a rigger does not meet the criteria, they must be supervised by a qualified rigger when performing rigging activities.
Why These Standards are Important to Understand
It is necessary for the employer and its employees to understand which standards their business falls under, and if the standards can change depending on the type of work they perform. The standards were created to make sure the working environment is safe. Although they may seem self-explanatory or information-dense, they are there to protect companies and their employees.
According to a study by Jimmy Don Wiethorn, Ph.D., of the accidents caused by human error, 26% of the accidents were due to the crane operator. 67% of the accidents were due to other crane personnel, mechanical related. This is why it is important to properly train the crane personnel in addition to the operator.
A trainee may learn how to properly operate a crane or rig a piece of equipment, but there is a high chance they are not learning to the standard. Classroom training focuses on safe practices, which is why it is highly recommended. Here at CICB, we provide classroom training for mobile cranes, rigging, inspections, and much more. We offer both qualification and certification courses, to ensure your business is following the standards.
For a visual representation of these standards, please see our infographics below.