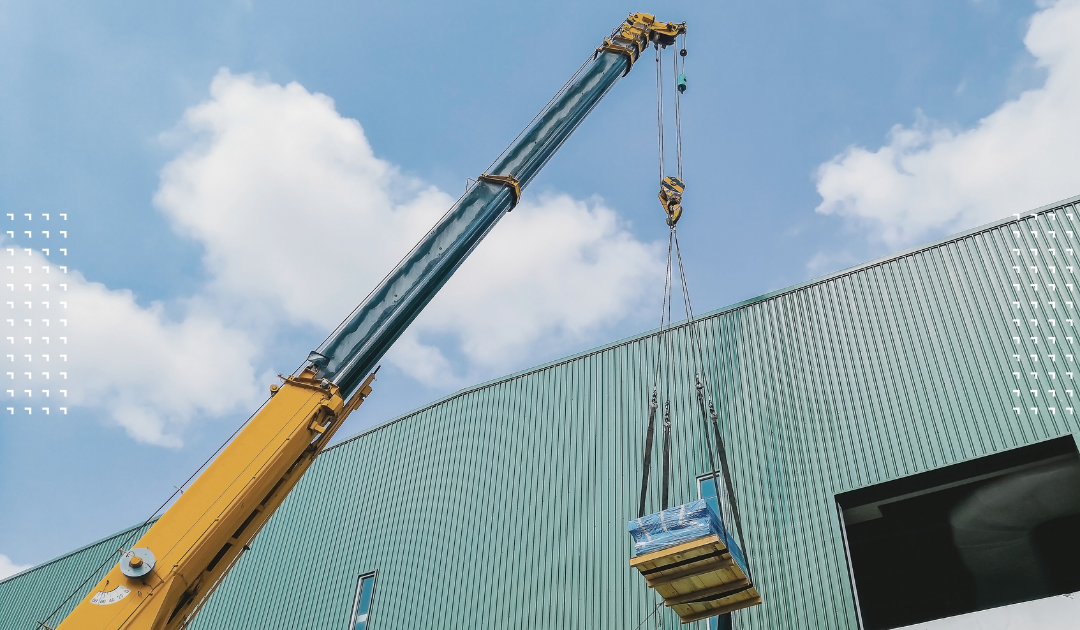
The Second Critical Challenge Facing Every Owner & Manager in The Crane & Lifting Industry Today – A Series
This is challenge number two in our five-part series.
As the lifting and crane industry continues to grow, so do the complexities surrounding safety regulations. OSHA (Occupational Safety and Health Administration) has significantly ramped up its enforcement efforts over the years, creating an environment of heightened scrutiny for businesses operating in this space. As regulations evolve and enforcement intensifies, owners and managers must navigate the challenges of maintaining compliance while mitigating the risks of costly violations and fines.
OSHA’s Increasing Focus on Enforcement
In 2010, Secretary of Labor Hilda Solis made a defining announcement, signaling a shift in the Department of Labor’s approach. She committed to a greater focus on enforcement, moving away from a primary emphasis on education and outreach. This marked the beginning of an era of heightened scrutiny and more rigorous enforcement by OSHA.
The results were immediate: fines from OSHA saw a significant increase in 2010, rising from $156 million in 2009 to $192 million in 2010. Fast forward a decade, and OSHA’s enforcement efforts have only intensified, with total fines hitting a record high of $331 million in 2022.
Trends in OSHA Enforcement
Despite a general decline in the number of OSHA citations over the past two decades, violations have been steadily increasing. A particularly concerning trend is the increase in the cost per violation, which has risen more than 3.5 times between 1992 and 2022. This figure does not even account for the additional legal costs involved in litigation and settlements, which can add significant financial burden to businesses.
In early 2023, OSHA introduced a new memorandum concerning Instance-by-Instance (IBI) citations for serious violations. This change means that, moving forward, each individual instance of non-compliance will result in its own citation, rather than grouping multiple instances under a single citation. This shift could significantly increase the number of citations a company faces if they fail to maintain strict compliance with regulations.
Focus on Construction: A High-Risk Industry
The construction industry continues to bear the brunt of OSHA’s scrutiny. In 2022, construction recorded the highest number of fatalities—1,069 workers lost their lives due to work-related incidents. Given the inherently dangerous nature of construction, this statistic is not entirely unexpected. However, it has prompted OSHA to take more proactive steps to improve safety within the sector.
For example, OSHA mandated that all crane operators be certified by December 10, 2018, in an effort to raise safety standards. In 2021, ASME updated the B30.5 standards, requiring at least one qualified rigger for lifting operations involving mobile cranes. Employers are now tasked with ensuring that their teams comply with these standards.
A Common Pitfall: Documented Monthly Inspections
One of the most commonly cited violations in the crane and lifting industry involves failure to comply with OSHA’s inspection and documentation requirements. Regular and thorough inspections are essential to ensure the safety of lifting operations and prevent costly penalties.
Crane inspections fall into two categories:
- Need-based inspections:
- Initial
- After modifications
- After repair
- Post-assembly
- Reinstallation
- Return to service
- Time-based inspections:
- Daily or shift inspections
- Monthly inspections
- Annual inspections
Failing to complete these inspections—and to document them properly—can result in fines and potential legal ramifications.
Solution: Frequent Training to Enhance Safety and Compliance
A proactive approach to training and certification is the key to minimizing safety risks, improving employee morale, and boosting productivity. Frequent training not only helps to prevent accidents but also contributes to extending the life of your equipment by ensuring it is used correctly and safely.
OSHA’s Minimum Training and Certification Requirements
OSHA mandates that employers ensure their employees are properly trained and qualified to operate certain types of equipment. Training requirements differ based on the equipment type and the industry in which the equipment is being used.
- Crane Operators: In the construction sector, crane operators must be certified by a nationally recognized accreditation agency, such as the NCCCO (National Commission for the Certification of Crane Operators). In other industries, employers are responsible for ensuring operators meet OSHA’s qualification standards.
- Riggers: A qualified rigger must always be present during rigging activities. If a crane operator is acting as the rigger, they must also meet the necessary qualification standards.
- Crane Inspectors: Crane inspectors must be qualified and competent to conduct thorough inspections of cranes to ensure their safety and compliance with OSHA standards.
- Lift Directors and Signalpersons: A lift director must be competent and qualified to direct lifts. Additionally, signalpersons, who are responsible for communicating during crane operations, must meet OSHA’s qualification requirements.
- Heavy Equipment Operators: Employers must ensure that all heavy equipment operators are instructed on the recognition and avoidance of unsafe conditions. Proper training helps to eliminate potential hazards, reducing the risk of injuries or fatalities.
Achieving Certification Through CCO
The Crane, Rigging, and Lift Industry can benefit significantly from certification programs such as the CCO (Crane Certification Organization). Earning CCO certification provides numerous benefits, including:
- Enhanced Safety Standards: Certified operators are better equipped to adhere to safety protocols.
- Consistency Across the Industry: Certification ensures that operators meet consistent standards across the field.
- Professional Recognition: Certification provides credibility, fostering trust with employers and clients alike.
- Regulatory Compliance: Certification helps ensure compliance with OSHA regulations, reducing the risk of fines and penalties.
- Increased Job Opportunities: Certified professionals have access to more job opportunities, benefiting both employees and employers.
CCO works with leading credentialing organizations like the International Assessment Institute (IAI) and maintains national accreditation with the ANSI National Accreditation Board (ANAB). These partnerships ensure that CCO certification remains a gold standard in the crane and lifting industry.
Conclusion
As OSHA regulations continue to evolve, business owners and managers in the crane and lifting industry must prioritize compliance to avoid the significant costs of non-compliance. By investing in training, certification, and thorough inspection processes, businesses can mitigate risks, improve safety, and ultimately strengthen their bottom line. With increased enforcement on the horizon, now is the time to ensure your team is fully prepared to meet OSHA’s demanding standards.